Pre-drywall preparation involves completing critical tasks that ensure the structural, functional, and aesthetic integrity of a building. These steps include securing utilities, installing insulation, and meeting inspection requirements before drywall installation begins.
Definition and Importance
Pre-drywall preparation is the process of addressing foundational tasks such as electrical wiring, plumbing, HVAC systems, and structural adjustments. It ensures that once the drywall is installed, systems are functional, compliant, and optimized for long-term durability.
Consequences of Skipping Pre-Drywall Tasks
Failing to complete pre-drywall tasks can lead to inspection failures, costly repairs, and system inefficiencies. For instance, a misaligned electrical box can render outlets inaccessible, while improper insulation placement may increase energy costs by up to 30%, according to a 2021 study by the Department of Energy.
Overview of Tasks
The primary steps before drywall installation include:
- Completing utility installations (electrical, plumbing, HVAC).
- Installing and inspecting insulation for energy efficiency.
- Ensuring blocking is in place for fixtures and shelves.
- Verifying measurements and spacing for structural components.
- Conducting pre-drywall inspections to ensure code compliance.
Tools and Materials Required
- Electrical tester: For verifying wiring connections.
- Pipe cutter: For plumbing adjustments.
- Staple gun: For securing insulation.
- Measuring tape: For precise placements.
- Inspection checklist: To ensure no step is overlooked.
Summary Table
Task Name | Purpose | Tools Needed | Key Steps | Time Estimate | Common Mistakes | Inspection Focus |
---|---|---|---|---|---|---|
Electrical Setup | Ensure functional wiring | Tester, wire strippers | Secure boxes, align wiring | 2–3 hours | Misaligned boxes | Wiring alignment |
Plumbing Adjustments | Prevent leaks, ensure connections | Pipe cutter, sealant | Test pipes, check valves | 3–4 hours | Skipped pressure tests | Leak detection |
Insulation Placement | Improve energy efficiency | Staple gun, tape | Measure, cut, secure insulation | 1–2 hours | Gaps or improper fitting | Insulation continuity |
Blocking Installation | Support fixtures, shelves | Drill, screws | Install blocks, secure tightly | 1–2 hours | Incorrect block spacing | Block stability |
Inspection Preparation | Ensure compliance with codes | Checklist | Verify all systems are ready | 2–3 hours | Overlooked steps | Comprehensive checks |
Each step in the pre-drywall process contributes to the overall success of the project. Proper preparation ensures the functionality of systems, reduces future maintenance needs, and provides a robust foundation for the finished interior.
Here’s What Needs to Be Done Before Drywall
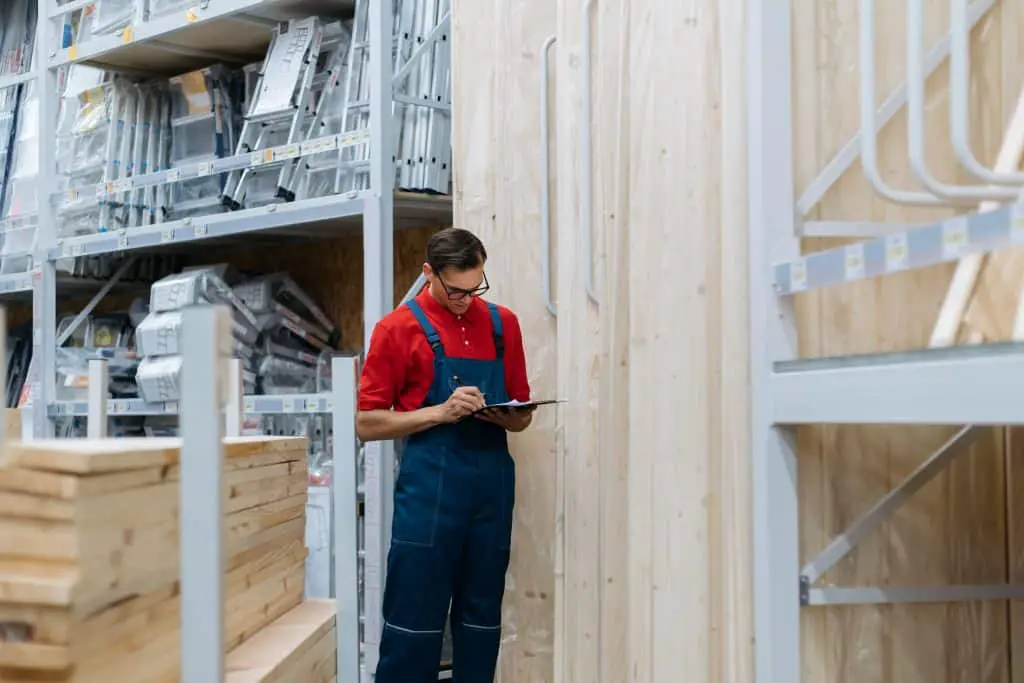
Before drywall installation, it is essential to complete a series of preparatory tasks that ensure structural integrity, system functionality, and compliance with building codes. Each step directly affects the quality and longevity of the finished walls and ceilings.
1. Electrical Systems Preparation
What needs to be done?
Electrical systems must be fully installed and tested before drywall. This includes securing wiring, aligning electrical boxes, and ensuring connections are functional.
Why is it important?
Improperly placed electrical boxes can lead to inaccessible outlets or switches. According to a 2020 report by the National Electrical Contractors Association, correcting misaligned boxes after drywall installation increases costs by 40%.
Steps to complete this task:
- Position and secure electrical boxes flush with the planned drywall surface.
- Test wiring connections using a multimeter.
- Label circuits for easier troubleshooting post-installation.
2. Plumbing Systems Inspection
What needs to be done?
Plumbing lines must be installed, tested, and secured. Ensure no leaks are present and that all connections are insulated if needed.
Why is it important?
Undetected leaks can lead to water damage. A study by the American Society of Plumbing Engineers (2022) found that 70% of water-related issues arise from missed pre-drywall inspections.
Steps to complete this task:
- Pressure test pipes for leaks.
- Secure pipes using brackets to prevent shifting.
- Insulate exposed pipes in colder regions to prevent freezing.
3. HVAC System Setup
What needs to be done?
HVAC ducts, vents, and connections must be inspected and secured. Placement of these components should align with architectural plans.
Why is it important?
Poorly aligned HVAC systems can lead to uneven heating or cooling. Research from ASHRAE (American Society of Heating, Refrigerating and Air-Conditioning Engineers, 2021) shows proper duct alignment can improve energy efficiency by 25%.
Steps to complete this task:
- Secure ductwork to prevent movement during drywall installation.
- Ensure vents are aligned with planned openings.
- Check for airflow obstructions.
4. Blocking Installation
What needs to be done?
Blocking must be installed to support future fixtures, shelves, or cabinetry.
Why is it important?
Blocking provides the structural foundation for mounted items. Without proper blocking, walls can buckle under the weight of fixtures.
Steps to complete this task:
- Measure and mark placements for fixtures.
- Secure wooden blocks between studs using screws.
- Test stability by applying pressure to each block.
5. Insulation Placement
What needs to be done?
Insulation should be measured, cut, and installed between studs and joists to improve energy efficiency.
Why is it important?
Proper insulation can reduce energy bills by up to 30%, according to the U.S. Department of Energy. It also helps maintain consistent indoor temperatures and reduces noise transfer.
Steps to complete this task:
- Choose the appropriate insulation type for each area (e.g., fiberglass, foam, or spray).
- Fill all gaps, ensuring no voids between studs.
- Secure insulation using a staple gun or adhesive.
6. Inspection Preparation
What needs to be done?
Complete a final walkthrough to ensure all systems meet building codes and are ready for drywall.
Why is it important?
Inspections ensure compliance with local codes and prevent delays in the project. According to the International Code Council (2021), failing a pre-drywall inspection can delay projects by 2–3 weeks on average.
Steps to complete this task:
- Use a checklist to verify all systems are complete.
- Conduct a mock inspection to identify potential issues.
- Address all flagged areas before the official inspection.
Do and Don’ts of Pre-Drywall Installation
Pre-drywall installation involves several critical steps that determine the success and efficiency of the finished construction. Following best practices while avoiding common mistakes ensures that all systems function correctly and inspections are passed smoothly.
Do: Finalize All Plans
Finalize architectural and system plans before starting pre-drywall tasks. Confirm placement of electrical boxes, plumbing lines, HVAC vents, and blocking.
- Why it matters: Revisions after drywall can cost up to 50% more than pre-drywall changes, according to a 2021 report from the National Association of Home Builders (NAHB).
- Best practice: Mark all placements on walls and ceilings for clarity.
Don’t: Skip Inspections
Never proceed with drywall installation without conducting a thorough pre-drywall inspection.
- Why it matters: Failing an inspection can delay projects by several weeks, costing both time and money.
- Common mistake: Overlooking minor issues such as misaligned electrical boxes or untested plumbing connections.
Do: Take Photos of Walls and Ceilings
Document the placement of wires, pipes, and structural elements before covering them with drywall.
- Why it matters: Photos help locate hidden systems during future renovations or repairs.
- Best practice: Use wide-angle and close-up shots for comprehensive coverage.
Don’t: Assume All Systems Are Installed Correctly
Never assume that all contractors have completed their work accurately. Conduct a detailed walkthrough before inspection.
- Why it matters: Small oversights, such as missing insulation or unsecured wires, can result in inspection failures.
- Common mistake: Relying solely on contractors without cross-checking their work.
Do: Use High-Quality Materials
Invest in durable materials for blocking, insulation, and utility systems to prevent future failures.
- Why it matters: High-quality materials reduce the need for repairs and increase the building’s overall lifespan.
- Best practice: Select materials rated for your specific climate and construction needs.
Don’t: Rush the Process
Avoid hurrying through pre-drywall preparation to meet deadlines. Each task requires careful attention to detail.
- Why it matters: A rushed job often results in costly mistakes, such as improperly secured pipes or misaligned HVAC ducts.
- Common mistake: Skipping final checks to save time.
Do: Ask Questions
Engage with your builder or contractor to clarify any uncertainties about placements, materials, or processes.
- Why it matters: Miscommunication is a leading cause of errors in pre-drywall preparation.
- Best practice: Create a list of questions and address them during site walkthroughs.
Don’t: Overlook Safety Measures
Ensure the work site is safe for contractors and inspectors by removing debris and securing loose materials.
- Why it matters: Unsafe sites can lead to accidents, project delays, and even legal liabilities.
- Common mistake: Leaving tools and materials scattered across the workspace.
Summary Checklist
Do | Don’t |
---|---|
Finalize all plans | Skip inspections |
Take photos of walls and ceilings | Assume all systems are installed correctly |
Use high-quality materials | Rush the process |
Ask questions | Overlook safety measures |
FAQs
Addressing frequently asked questions about pre-drywall preparation ensures clarity and provides solutions to common concerns. Here are the definitive answers to key queries:
Do You Drywall the Ceiling or Walls First?
Drywall the ceiling before the walls.
- Why it matters: Installing drywall on the ceiling first provides structural support for the wall panels, preventing them from sagging.
- Evidence: According to a 2020 study by the International Association of Drywall Contractors, ceiling-first installation reduces joint stress by 25%.
Do You Do Flooring or Drywall First?
Install drywall before flooring.
- Why it matters: Drywall installation generates dust and debris that can damage finished flooring. Installing drywall first also allows for cleaner baseboard installations.
- Best practice: Cover the subfloor with protective material during drywall installation to prevent damage.
Can You Drywall Over Electrical Junction Boxes?
No, electrical junction boxes must remain accessible.
- Why it matters: Covering junction boxes violates electrical codes and creates safety hazards. Junction boxes must remain flush with the drywall surface for easy access during repairs or upgrades.
- Evidence: The National Electrical Code (NEC) mandates that all electrical boxes must be accessible at all times.
What Happens If I Skip a Pre-Drywall Inspection?
Skipping a pre-drywall inspection can lead to code violations, structural issues, and increased repair costs.
- Why it matters: Inspections ensure that all systems are installed correctly and comply with local regulations.
- Cost implications: A missed inspection could result in fines and a 30% increase in post-drywall correction costs, according to the 2021 International Code Compliance Report.
How Do I Document Pre-Drywall Progress?
Take detailed photos of all systems before covering them with drywall.
- Why it matters: Documentation simplifies future repairs, renovations, or inspections by providing a clear record of what lies behind the walls.
- Best practice: Use timestamped photos and organize them by room for easy reference.
Is It Necessary to Seal Insulation Before Drywall?
Yes, insulation must be sealed to prevent air leaks and ensure energy efficiency.
- Why it matters: Properly sealed insulation reduces energy loss by up to 15%, according to the U.S. Department of Energy.
- Steps: Use spray foam or adhesive tape to secure the edges and prevent gaps.